This underground tank removal guide aims to answer frequently asked questions surrounding the safe emptying, cleaning and subsequent removal of underground fuel and oil storage tanks. Underground storage tanks are found in a multitude of locations; however in this scenario, we’ll be studying a fuel filling station being decommissioned by JWH Tanks.
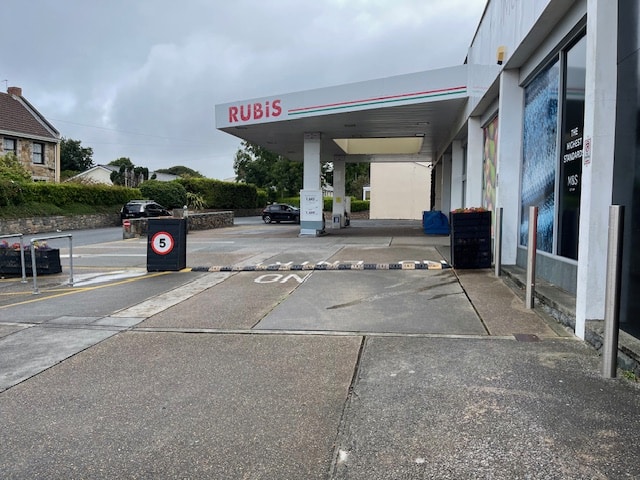
Contractors, Notifications & Documentation:
Selecting a Contractor:
When selecting a contractor, there are a number of simple checks that can be made to assess competence, including checking the accreditations of the company, not just on their own website, but through the awarding body mentioned. Most have the option to confirm if the contractor has that certificate. Speak to the local regulatory bodies, e.g., Trading Standards or The Fire Service, particularly when dealing with petrol. Finally, when speaking to a potential contractor, ask as many questions as possible to ensure they have the knowledge, experience and appropriate attitude towards safety. Ideally, you should be able to speak to an engineer or technical expert within that company to ask questions and gain the information you need. Be aware that many companies simply subcontract this work out, so a glossy website does not always mean they will be conducting the work themselves.
Notifications:
When considering the removal of an underground fuel storage tank, a competent contractor must be selected, who holds the ability to produce concise and relevant documentation to be issued to both the client, along with other stakeholders such as regulatory bodies in the form of Petroleum Licensing Officers, the Health & Safety Executive, and the Environment Agency. The number of regulatory bodies contacted and the array of documents issued will depend on factors such as the product being stored, the scale of the project, client requirements and environmental sensitivity considerations.
Documentation:
Samples of documents issued prior to commencing work will be a safe system of work, including method statement, risk and COSHH assessments, training records, construction phase plan, emergency procedures, waste licensing information, equipment maintenance records, and insurance confirmation. These documents should be produced following a site survey by a safety specialist from within the organisation carrying out the work.
On this particular occasion, although the project wasn’t F10 notifiable in size or scale, our client requested that we notify the local health & safety department via an F10 submission, in addition to the petroleum licensing authority. Our in-house safety team duly obliged, and submitted the forms along with a construction phase plan and details of our safe system of work. This was all approved by the regulatory bodies alongside our client’s appointed safety consultant, thus allowing the next phase of the project to begin.
Getting Underway:
As with any work site, the area must be made safe for both the surrounding public, but also for those working on site. This was achieved in a number of ways:
Access & Egress – Access to the site should be strictly controlled to ensure that no un-authorised personnel can gain access, as this can jeopardise the safety of everybdy on site. Suitable methods of securing access are by using heras style fencing and wooden hoarding.
Site Preparation – As we were to undertake excavations on site, it was essential to conduct a full utility scan of the area, compare this with any original documentation available and make any required isolations prior to breaking ground. The details of the drawings and surveys are also included in the permit to dig to ensure that all involved parties are aware of service locations.
During the project, the contractor should keep you informed by issuing documents such as daily job sheets, gas free certificates, isolation certificates, tank cleaning reports, waste notes, copies of permits and where required, information relating to regulatory body involvement.
In the paragraphs below, we’ll outline what information would be issued to the client at each stage. Where any aspect of the work is subcontracted, your appointed contractor should be able to demonstrate that they are monitoring the work of their appointed subcontractor.
Tank Emptying and Cleaning
In this underground tank removal guide, we discuss a number of factors to safely complete the task at hand. There is possibly no more important safety factor, particularly when working with petrol, than ensuring the tanks are clean and gas free. On this particular site, the client had a close working relationship with the local fuel supplier, and was able to facilitate an uplift in the days prior to our team attending, leaving only a very small amout of fuel in the base of the tanks. Prior to extracting this fuel, any product in the lines must also be blown back to ensure that no product remains on site.
During this stage, any ancillary equipment such as dispensing pumps and pipework within the chambers can be disconnected and removed, thus reducing the risk of any dripping back into the tanks.
With the tanks cleaned, atmospheric monitoring can be conducted to ensure that each tank is gas free, prior to gas free certificates being issued. When working with petrol, certificates must be renewed every 24 hours as a minimum, however at JWH Tanks, we like to ensure that each day begins with further monitoring and the issuing of new gas free certification.
Canopy Dismantling & Removal:
The next phase of this project is to dismantle and remove the forecourt canopy. This is being conducted as the client is extending the footprint of the adjacent store, and also because the tanks are situated beneath the conopy, thus making the underground tank removal very difficult.
As mentioned in the previous section, the cleaning of the tanks becomes critical at this point, as the dismantling of the canopy will involve some cutting, which can only be safely performed with all tanks on site under a gas free certificate. This particular canopy was different to many found across the country as it was attached to the building front, thus requiring extreme care when dismantling to ensure no damage to the fabric of the building.
Underground Tank Removal
With the tanks clean and gas free and the canopy now removed, space is available on site to begin excavating the underground tanks for eventual removal and disposal. As mentioned previously, the entire process must follow a prescribed safe system of work, that must be approved by all relevant stakeholders. This will involve following the method statement, applying the control measures identified in the accompanying risk assessments, then extending this system by issuing permits to carry out high risk tasks, such as confined space working, use of hot works and excavation equipment.
Items essential to the issuing of a permit to excavate will include ensuring that all possible checks have been made to identify underground services, ensuring the excavation equipment has been inspected to the required standard, the operator is both competent, trained and insured to do so, all tanks have valid gas free certificates, an exclusion zone is in operation and that this information has been communicated to all parties.
With the permit in place, the underground tank removal can commence safely, with the permit being closed and then reopened each day until the excavation has been completed.
Should ground validation be undertaken as part of the underground tank removal, this must be undertaken by a qualified Geo-technical specialist, using ground sample information analysed by a UKAS accredited laboratory.
Ground Validation
As part of the underground tank removal process, the identification and subsequent removal of any contaminated soils should be undertaken. This will be conducted by a qualified geo-technical specialist, but normally utilising the same excavation equipment used to extract the underground tanks.
Should any areas of concern be highlighted, impacted ground should be removed and placed in a quarantined area on site, using protective sheeting to ensure the no further impacting of soils can occur. The impacted soils will be subjected to further screening in the form of waste acceptance criteria (WAC) testing, in order to find a suitable treatment or disposal point.
Once completed, the excavation can then be backfilled with clean imported hardcore, either pending further works e.g. just leaving the site safe, or involving compacting at defined intervals should resurfacing be planned.
Completion:
Finally, upon completion, the contractor must provide the client with any legal documents, such as a duty of care note for any inert waste removed, or a hazardous waste consignment note for any contaminated waste, including the consignee certificate to inform the client of the final disposal location of the waste.
The contractor should also be able to provide certification to detail what infrastructure was removed or, in some cases, made safe in situ.
As mentioned at the beginning of this underground tank removal guide, please ensure you ask any potential contractor plenty of questions about how they plan to undertake the work, not just how much it costs.
Further external information can be found at: Gov.uk – Prevent groundwater pollution from underground fuel storage tanks
Further info on our services can be found at: Underground tank cleaning